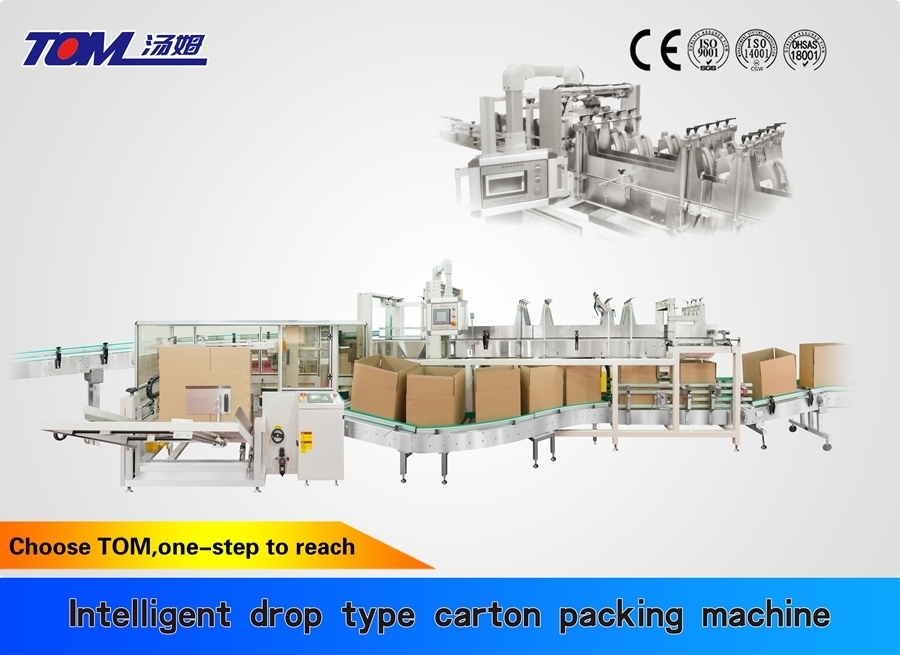
Automatic drop type carton packer/high speed
Model: ZDP-1NA
Minimum order quantity: 1set
Payment term: T/T, L/C
Delivery time: 45 working days
Delivery port: Shanghai, China
Packing: Non-fumigation wooden case inserted Iron Shelf, suitable for long time sea delivery
Certificate: ISO9001:2000, ISO14001, OHSAS18001, CE, CO
Standard: Meet GMP standard
Cleaning: Easy cleaning
Place of Origin: China (Mainland)
Service: Engineer is available to install and debug the equipment at customer site.
In order to ensure the correct coding of the box and the barrel, the servo motor is used to separate the lanes to avoid the situation of lane division errors or inconsistencies due to other factors. The front section is equipped with a steering mechanism, which can be packed according to the code.


The product enters the grid form mechanism through the lane dividing system, and the photoelectric feedback bottle lacking signal, then the lane dividing system swings to the column of the bottle lacking to transport the bottle inlet. When the photoelectric feedback bottle full signal, then stops conveying. Can meet a variety of ways such as single column, double column and 3x2 column. Each column has a photoelectric detection feedback device that can quickly and accurately feedback whether there is a lack of bottle or full bottle status.
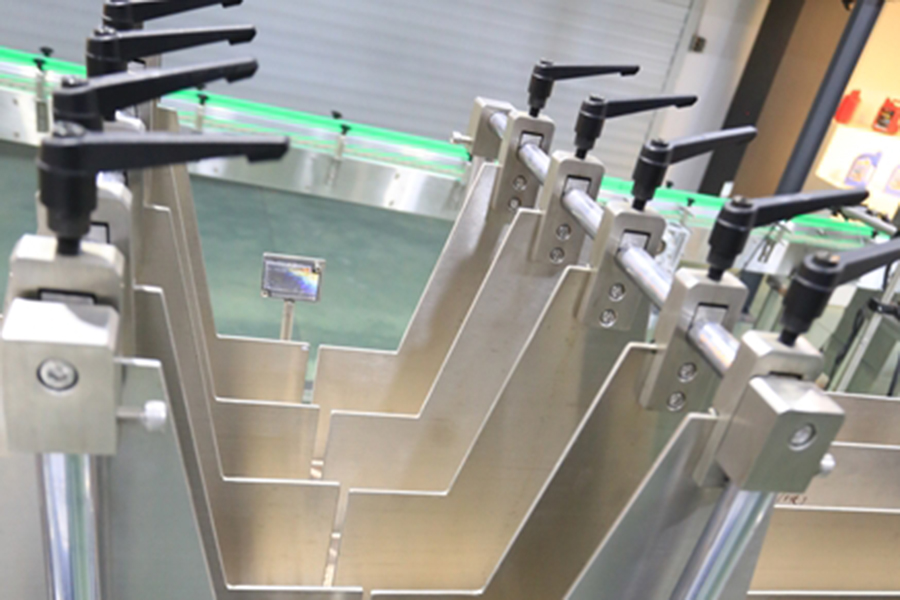
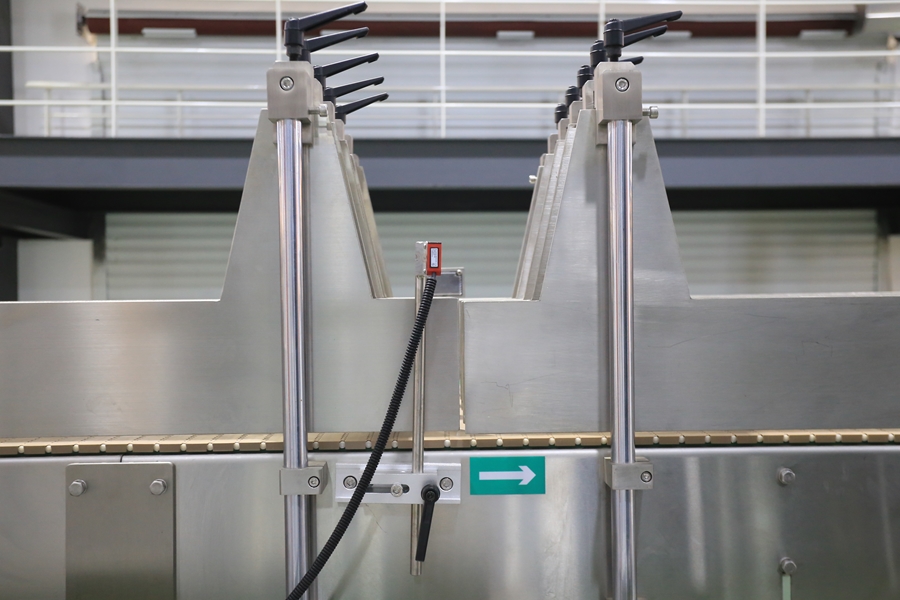
The box falling location is equipped with a retaining pressure plate to prevent the bottle continuing to be transported to the packing position during packing other bottles, to ensure the stability and efficiency of packing. The loading port is equipped with a guiding mold to accurately feed the bottle into the carton for packing.

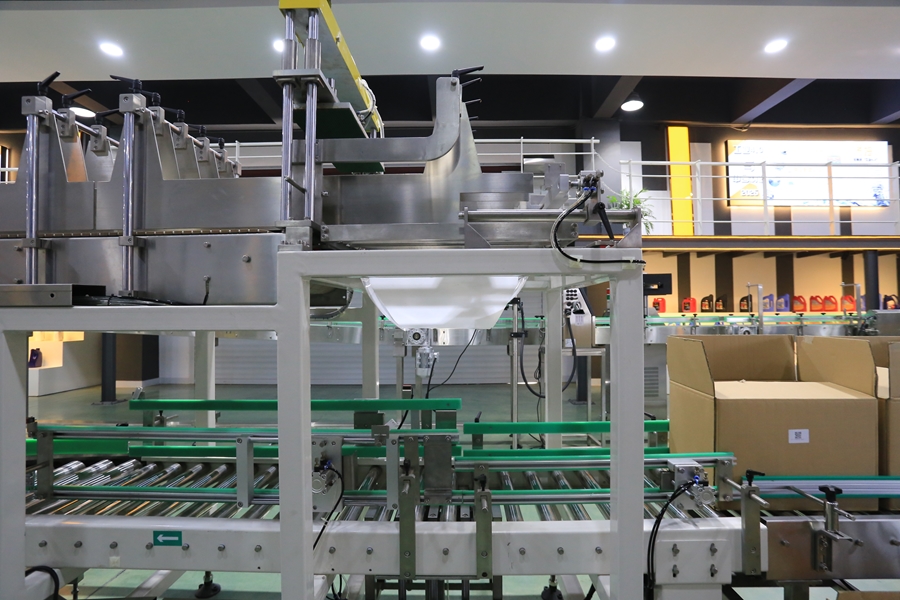
The bottom of the carton is equipped with a jack-up cylinder, which rises when packing, and slowly falls during the packing process, reducing the impact force and preventing the carton from being damaged.
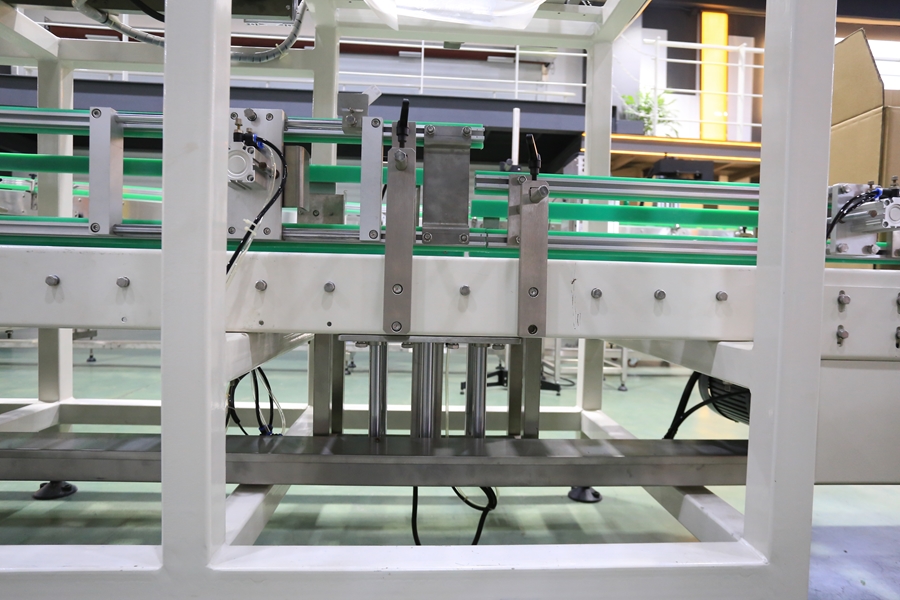
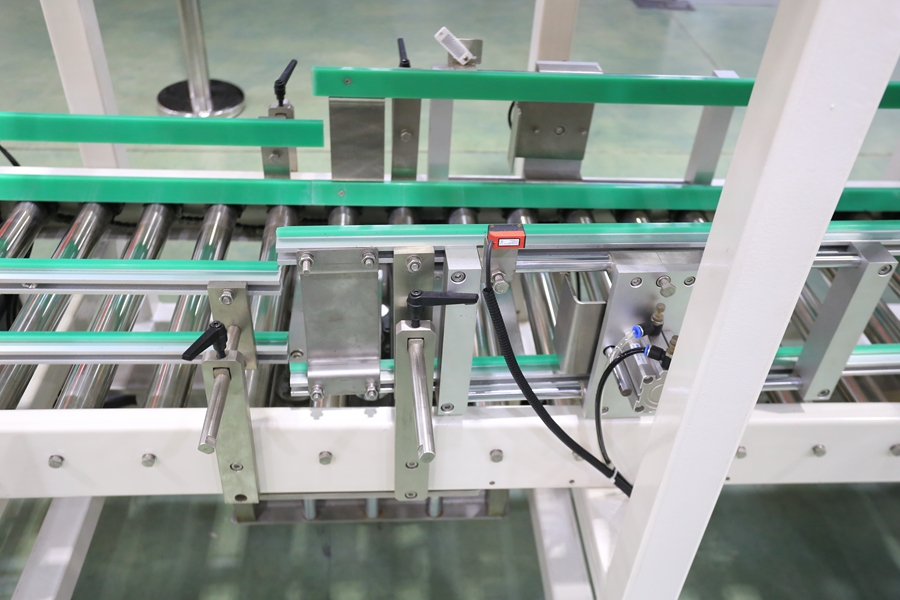
1.Inlet bottle lacking detecting sensor
The machine installed bottle lack photoelectric detection and bottle blocking photoelectric detection, when the bottle lack in inlet place, machine will stop and alarm automatically; when inlet bottle enough, machine will start running automatically; when the bottle blocking in outlet place, machine will stop and alarm automatically; when bottle blocking relieve, machine will start running automatically;
2. Conveyor and drip gutter:
the conveyors before filling and after filling equipped with drip gutter also, to prevent liquid drop on ground and pollution workshop.
3.Oil-water separator:
The oil-water separator is installed before inlet main pipe, can prolong the service life of pneumatic components, main machine with air pressure protection alarm device, when the air pressure is over high or over low, main machine will stop automatically and alarm.
4.Protection door:
All doors on the machine are equipped with safety door switches and full range of interlock control. If any door is opened, the machine cannot start or stop automatically.
5.Cover lock:
All protection cover of machine is easily open and close, just press it and rotate, it is convenient for operate to make maintenance.
6. Jogging device:
The commissioning personnel can jog the equipment through the hand-held control box. The control box has the jog and emergency stop functions. The commissioning personnel can press the emergency stop button at any time even if it is debugged behind the equipment to prevent accidental injury.
7.Touch screen:
The support of touch screen adopts 360-degree rotatable bracket, which is easy to operate, simple and generous in appearance, strong in practicability, and gives the operator a kind of enjoyment at one's own will.
8.Electric box:
The electrical part are in top side of machine, can prevent water and material inside it, safety and environmental.
9.Cable trays:
simple structure, beautiful appearance, flexible configuration and convenient maintenance, so that the cables and air pipes on the site are not messy.